What factors affect the adhesion of aluminum foil wrapped with Lurex fabric during production?
The adhesion of aluminum foil wrapped with Lurex fabric during production is influenced by several factors. Ensuring strong and consistent adhesion is critical to the fabric's quality and longevity. Here are some key factors that affect the adhesion of aluminum foil during Lurex fabric production:
1. Choice of Adhesive: The type of adhesive used to bond the aluminum foil to the core thread is a critical factor. The adhesive must have good adhesion properties and be compatible with both the metallic foil and the core material (usually polyester or nylon). The choice of adhesive can significantly impact the strength of the bond.
2. Adhesive Application: The method and consistency of adhesive application play a crucial role in adhesion. Proper and uniform distribution of adhesive on the core thread is essential to ensure that the foil adheres evenly and securely. This can be achieved through precise coating and spreading techniques.
3. Adhesive Drying/Curing Time: The drying or curing time of the adhesive is essential to allow it to set and create a strong bond. The curing process may involve heat, pressure, or air-drying, depending on the specific adhesive used.
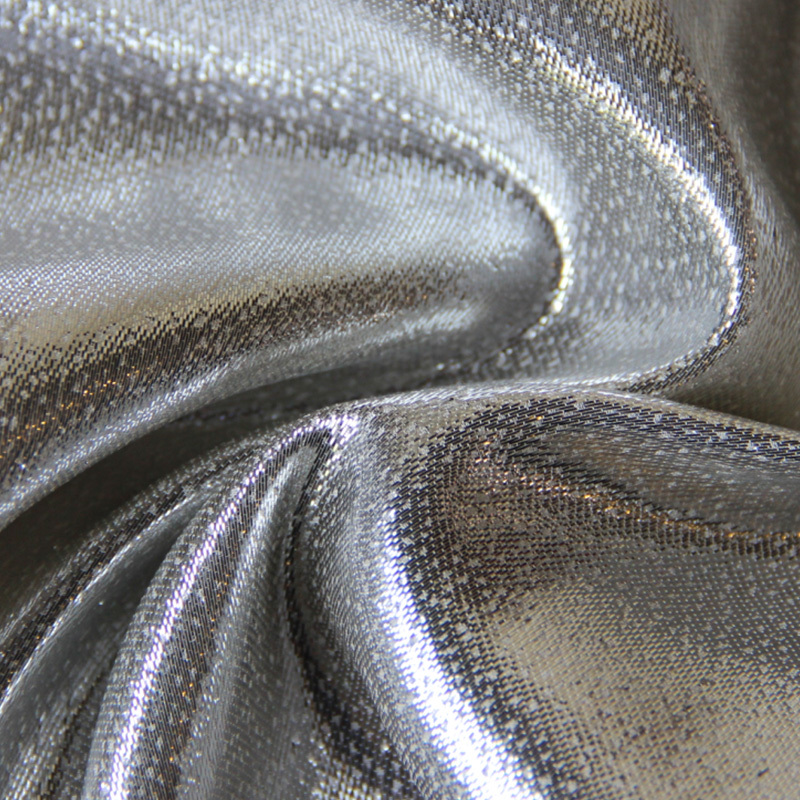
4. Core Thread Material: The type and condition of the core thread material affect adhesion. A clean and well-prepared core material provides a better surface for the adhesive to bond with. Additionally, the material's compatibility with the adhesive is important.
5. Temperature and Humidity: Environmental conditions during production can influence adhesion. Variations in temperature and humidity can affect the drying and curing processes of the adhesive. Maintaining stable conditions in the production area helps ensure consistent adhesion.
6. Pressure and Tension: Proper application of pressure and tension during the wrapping process is crucial. The right balance of pressure helps the foil adhere to the core thread evenly without gaps or air pockets. Tension control ensures that the foil is firmly pressed against the adhesive-coated thread.
7. Foil Thickness: The thickness of the aluminum foil can affect adhesion. Thicker foils may require more adhesive and pressure to bond effectively, while thinner foils may bond more easily.
8. Quality Control: Rigorous quality control measures, including inspections and tests, help identify and address adhesion issues during production. Any defects or weak bonds can be identified and rectified to maintain consistent quality.
9. Consistency in Materials: The consistency of the materials used, including the adhesive, foil, and core thread, is essential. Variations in material properties can lead to inconsistent adhesion.
10. Curing and Setting Process: The process used to cure or set the adhesive, such as the application of heat or pressure, should be carefully controlled to ensure a strong and durable bond.
Properly addressing these factors ensures that the aluminum foil adheres securely to the core thread, resulting in a Lurex fabric with a consistent and durable metallic appearance. Manufacturers often have proprietary methods and quality control measures to optimize the adhesion process.